Selecting the right hose for hydraulic oil systems is both a science and an art, bridging the gap between precision engineering and practical performance. In hydraulic systems, hoses play an indispensable role, acting as conduits for fluid transfer under high pressure. The importance of choosing the right type of hydraulic hose cannot be overstated, as it impacts everything from system efficiency to safety and lifespan.
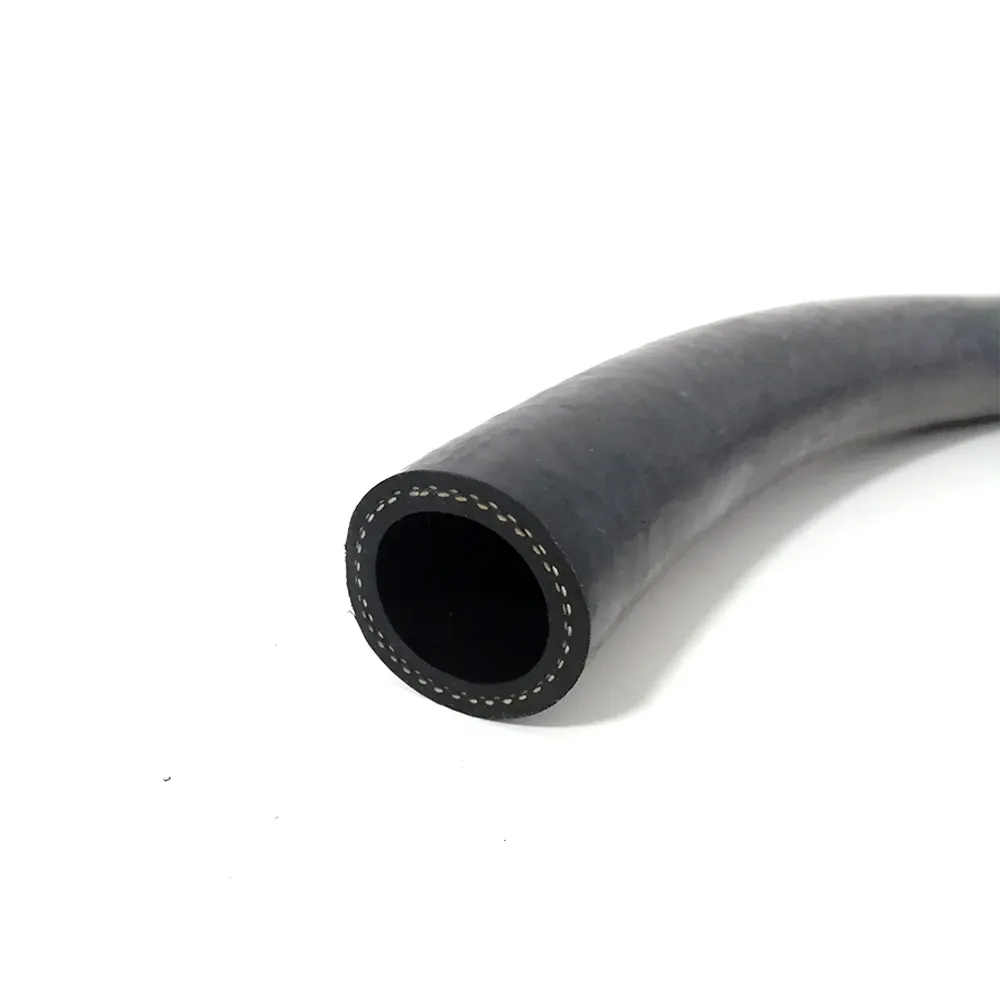
Hydraulic oil hoses come in various types and configurations, each designed for specific applications and pressure ratings. Among the primary considerations for any user or technician are the type of material used, pressure capacity, flexibility, and compatibility with the hydraulic fluid.
Firstly, understanding the material composition is critical. The most common materials used in hydraulic hoses are synthetic rubber, thermoplastics, and PTFE (polytetrafluoroethylene). Synthetic rubber hoses are favored for their flexibility and ability to handle diverse temperature ranges. They are often reinforced with braided steel or spiraled wire to withstand high pressures. Thermoplastic hoses, on the other hand, are lighter and can be chosen for applications requiring superior resistance to oil and chemicals. PTFE hoses are known for their exceptional durability and ability to operate in extreme temperature environments, making them suitable for specialized industrial applications.
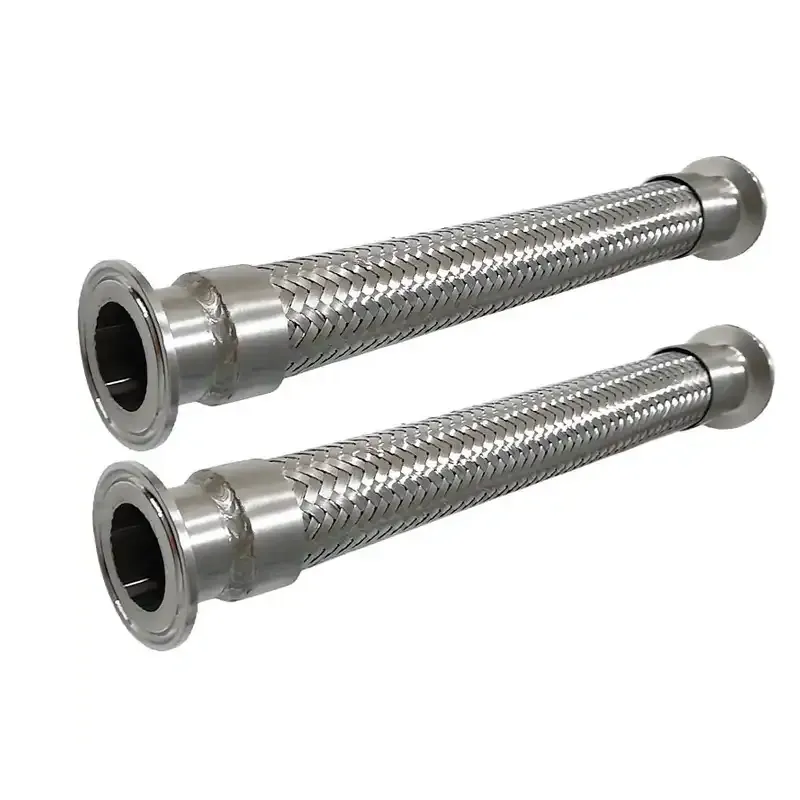
The pressure rating of a hose is another fundamental factor. Hydraulic systems can range from low to ultra-high pressure demands. It's essential to select a hose rated for your specific application needs to prevent failures. A hose designed to handle pressures of up to 3,000 PSI may suffice for common industrial applications, but in specialized machinery, like those used in mining or construction, a hose with a higher pressure threshold might be necessary.
Flexibility is also a key characteristic that should align with system requirements. The bend radius—how tight a hose can be bent without causing damage—is critical for installations with limited space. A more flexible hose can reduce installation time, decrease connection points, and, ultimately, lower the likelihood of leaks.
Compatibility with hydraulic oil is non-negotiable.
Not all hoses are compatible with all types of hydraulic fluids. An incompatible hose can degrade, leading to leaks and failure. Thus, confirming the chemical compatibility of a hose with the fluid used in your system is paramount. It's advisable to consult with manufacturers or references for compatibility charts.
hose for hydraulic oil
When considering expertise in hydraulic systems, understanding the intrinsic relationship between hoses and the other system components is vital. For example, fittings must be compatible in terms of size and material. A mismatch can lead to assembly failures or leaks, which can compromise system efficiency or safety.
From an authoritative standpoint, industry standards such as those from the Society of Automotive Engineers (SAE) or the International Organization for Standardization (ISO) should guide hose selection. Adherence to these standards ensures a basic level of quality and performance reliability.
Trustworthiness in choosing a supplier or manufacturer is yet another layer to consider. Opt for suppliers with established reputations and a proven track record in hydraulic systems. Their expertise will provide not only the right products but also essential guidance for installation and maintenance.
Real-life experiences underscore the importance of prevention and regular maintenance in ensuring the longevity of hydraulic hoses. Regular inspections for wear and tear, along with understanding the environmental conditions the hoses are exposed to, play crucial roles in pre-emptive maintenance strategies. Environmental factors like excessive heat, abrasives, or exposure to corrosive substances can dramatically reduce hose life.
In conclusion, the art of choosing the right hose for hydraulic oil encompasses a detailed understanding of materials, pressures, flexibility, compatibility, and standards. Leveraging expertise, securing reliable partners, and having a proactive maintenance strategy embedded in operational practices reflect in improved system reliability and efficiency. The right hose not only ensures the seamless operation of the hydraulic system but also significantly cuts down on downtime and replacement costs, contributing to the overarching goals of safety and operational excellence.